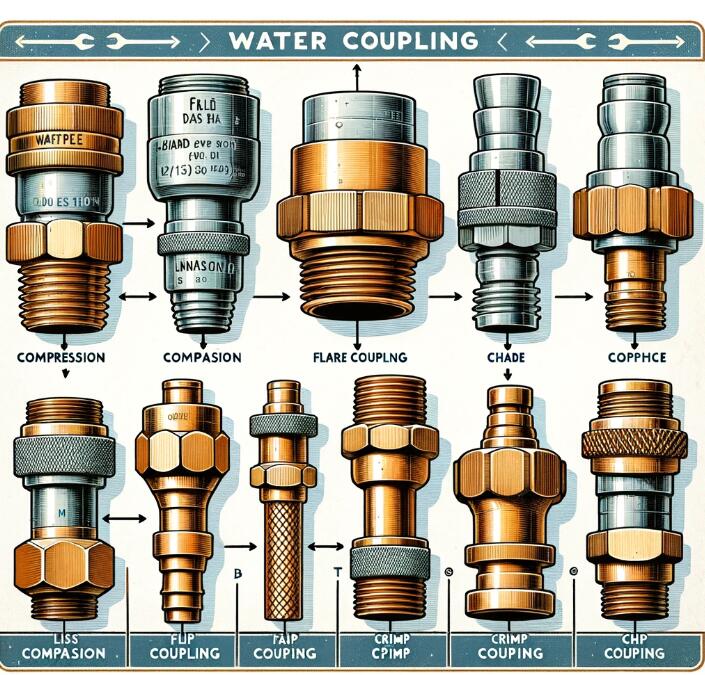
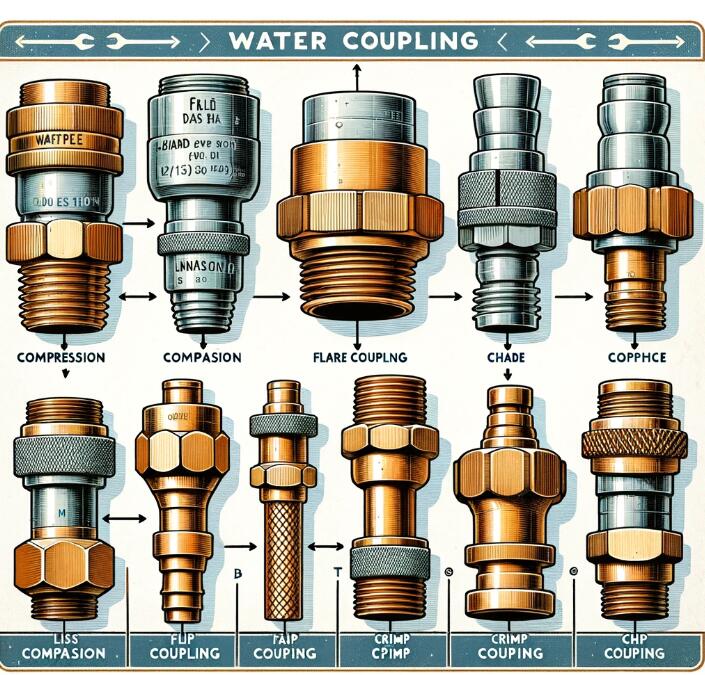
Unlocking Efficiency: A Comprehensive Guide to Quick Coupling Types
Welcome to our comprehensive guide on quick couplings, a pivotal component in many industrial and mechanical applications. Quick couplings, often understated, play a crucial role in ensuring efficient and secure connections in a variety of systems. This article aims to shed light on the different types of quick couplings and their vital applications across industries.
The Basics of Quick Couplings
Quick couplings are connectors used to join two parts of a system together, allowing for easy and quick connection or disconnection. A hallmark of these components is their ability to save time and reduce the need for tools during assembly or disassembly, making them indispensable in many fast-paced environments.
Importance in Industry
From hydraulic systems in construction machinery to pneumatic tools in manufacturing, quick couplings are the unsung heroes that maintain the flow of fluids or air. Their significance lies in their ability to maintain system integrity, prevent leaks, and ensure safety and efficiency in operations.
Types of Quick Couplings
Quick couplings come in various forms, each designed to cater to specific applications and media they convey. Here’s an overview of the most common types:
Hydraulic Couplings
Used primarily in high-pressure environments, hydraulic couplings are designed for excavators and other heavy machinery systems. They transfer hydraulic fluid under immense pressure without leaks or loss of fluid.
Pneumatic Couplings
Pneumatic couplings are tailored for air-powered systems. They are commonly found in manufacturing facilities where air tools are prevalent. These couplings are designed for quick and tight connectivity of air hoses while ensuring a tight seal.
Water Couplings
Water couplings find their usage in plumbing and irrigation systems. They are built to withstand different water pressures and provide secure connections in water transport systems.
Electrical Quick Couplings
Although less common, quick electrical couplings exist to provide fast and reliable electrical connections. These are typically used in modular electronics or equipment where frequent reconfiguration is required.
Material Considerations
The choice of material for quick couplings is pivotal and depends on the application:
- Brass: Offers good corrosion resistance and is commonly used in plumbing.
- Stainless Steel: Ideal for harsh environments, providing durability and resistance to corrosion.
- Plastic: A lightweight and cost-effective option suitable for less demanding applications.
Each material has its unique properties, and choosing the right one ensures the longevity and efficiency of the coupling system.
Connection Types and Mechanisms
Quick couplings can also be differentiated by their connection types and mechanisms:
Threaded vs. Non-threaded Couplings
Threaded couplings provide a secure connection by screwing onto mating threads, ideal for high-pressure applications. Non-threaded couplings, on the other hand, offer quicker connection and disconnection, suitable for applications where speed is essential.
Push-to-Connect Couplings
These couplings allow for a simple push-to-connect mechanism, vastly reducing the time and effort needed for connection. They are often used in systems where frequent disconnections are required.
Camlock Couplings
Camlock couplings are known for their ease of use, featuring a simple lever-locking mechanism. They are widely used in industries for transferring liquids and are particularly valued in agricultural and chemical applications.
Quick couplings are more than just connectors; they are vital components that enhance efficiency and safety in numerous systems. Understanding the different types of quick couplings, their materials, and connection mechanisms is crucial for selecting the right one for your application. We hope this guide provides useful information on quick couplings and helps you make informed decisions for your needs.
Selecting the Right Quick Coupling
Choosing the correct quick coupling is crucial for system efficiency and safety. Here are key factors to consider:
- Pressure Ratings: Ensure the coupling can withstand the system’s pressure requirements.
- Temperature: The coupling material and design must be suitable for operating temperatures.
- Fluid Type: Compatibility with the type of fluid (e.g., oil, water, air) is essential to prevent corrosion and leakage.
- Environment: Consider environmental factors such as exposure to chemicals or extreme conditions.
Choosing the right coupling is crucial for improving system performance and longevity.
Maintenance and Safety
Maintaining quick couplings is vital for system integrity and safety. Regular inspection for wear and tear, ensuring proper connection, and timely replacement of damaged parts are key practices. Additionally, always adhere to safety guidelines to prevent accidents, especially in high-pressure systems.
Innovations and Future Trends
The quick coupling industry is continually evolving with technological advancements. Innovations like smart couplings with integrated sensors for real-time monitoring and self-sealing couplings for enhanced safety are rising. The future trends point towards more automated, efficient, safer, and quick coupling systems, potentially revolutionizing various industrial applications.
Quick couplings are integral components that significantly impact the efficiency and safety of various systems. Understanding the types, materials, and application-specific requirements is key to selecting the right coupling. With technological advancements, the future of quick couplings looks promising, offering even more efficient and safer solutions.
This guide aims to thoroughly understand quick couplings, empowering professionals to make informed decisions in their respective fields. We encourage you to consider the discussed factors for optimal performance and safety in your systems.